Panel Fabrication
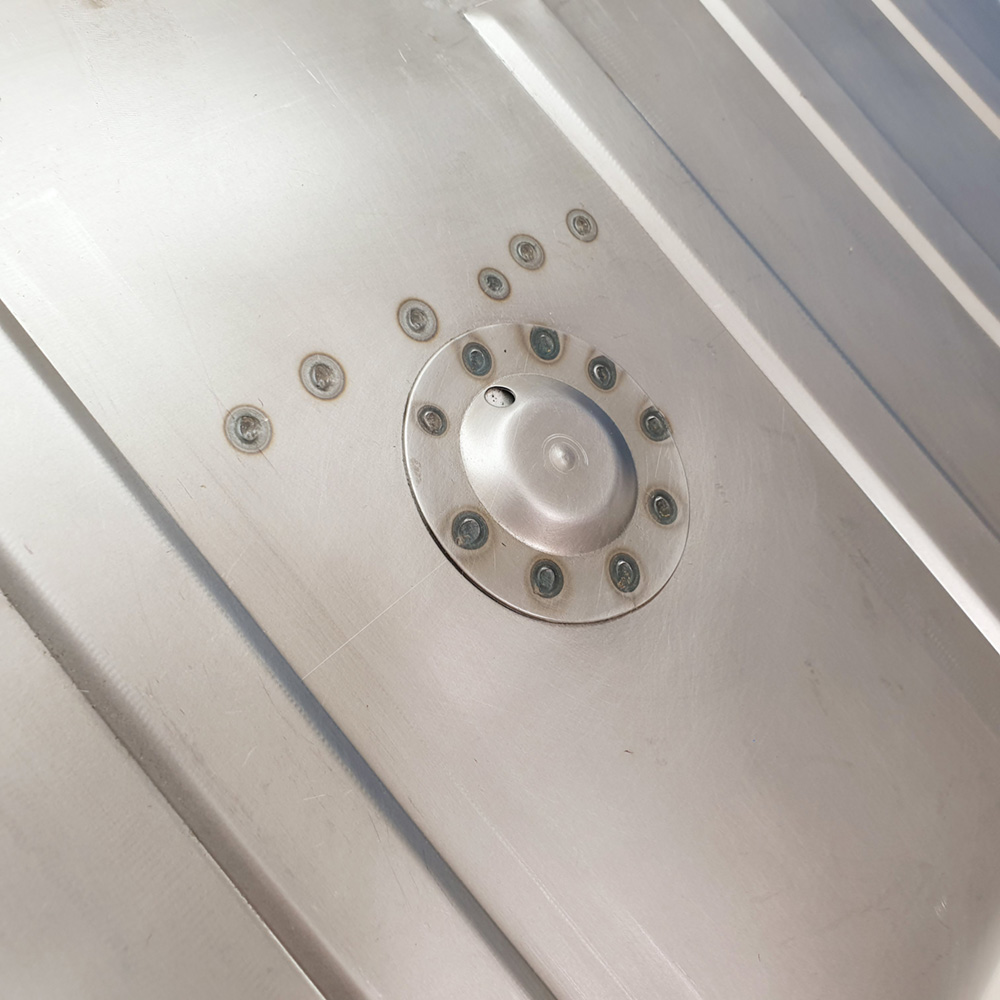
The tooling required to mass produce panels can be quite expensive and the remanufacturer would be more than likely only interested in high sales directly aimed towards classic cars that have a high production number and a good following of collectors. The good following criteria would usually be calculated back to a classic car manufacturer that is still around today and still quite successful. The brands like Porsche, Jaguar and Mercedes are prime candidates for this and the fact that they have all been very successful in the racing industry of the classic car era simply coincides with a classic car worth investing in.
Then of course there is these great brands of automakers that have produced beautiful classic cars but in very small production numbers. These cars might have been released at the very beginning of a certain model before the manufacturer realised it was going to be successful and changed quite a few panels and accents to the vehicle before it went into an increased production rate. These cars are not viable to invest in tooling cost for mass-produced reproduction panels, however as they are usually the ones that appreciate earlier than the higher production models, they are certainly worth restoring. I personally feel that they are the best cars to restore because of their little differences they have that make them unique to the masses. In this instance, the art of panel fabrication by hand comes into play to save these beautiful, classic, rare and unique sports cars for the many decades to come.
When manufacturers made their very first cars and prototypes every single panel within the car was made by hand, with old fashioned techniques that includes blocking hammers, sandbags, English wheel or Wheeling machine, folders, guillotines, swages, reciprocating hammers, shrinkers, stretchers and other hand operated machinery. To use these methods in early to mid 1900s was not seen so much as a skill or an art form as it is seen today, it was simply a job for many people day in, day out. Today it appears that has been glorified a little. Maybe this is Superman's fault, the man who could bend steel with his bare hands. I do enjoy the fact that this is one of my skills and enjoy the satisfaction of the end results every time. However, I'm not delusional, I am not Superman. I never wear my underwear on the outside… especially on a week day!
Fabricating a brand new panel starts with either, a drawing if it is quite basic and a series of straight folds, or for more elaborate panels, profiles in either cartridge paper or steel to mimic the shape and contours to pattern what is required.
To establish that your patterns are correct you must check them at the very minimum to both sides of the vehicle and if you have other models the same, check them as well. There is no substitute for having a multiple of the same panel for size and shape references to show a common data.
For a large panel you may need to decide where you are going to join the new panel sections in with the original existing panel or if you are going to fabricate a number of panels and join them all together with fusion welding to create one large panel that could then be spot welded to the body shell.
Next you would be considering what areas of the sheet metal or aluminium needs to be stretched out to create the beginning of the shape and contours desired. Stretching usually starts with hammering and blocking the panel into a sandbag. This is something you want to creep up on and avoid hammering too much shape into the panel because over-stretching and too much shape can be a lot of work to shrink back.
Once the blocking and hammering is close, the wheeling machine or planishing hammer will smooth it all out and give you your first glimpse of something resembling the panel your fabricating. Checking your patterns frequently will guide the amount of hammering and wheeling still to go. Swage lines and folds will follow and these can be done in swaging machines, folders, or even by hand with a swedge, hammers, dollies, chasers and sandbags.
In some instances, you know that you will be making more than one panel or even pairs of panels so the decision to make low cost tooling is recommended. It could be as simple as a couple of bits of wood or thick steel plate, precisely cut to a patterned shape that will aid in clamping the material in the middle and forming the edge around the profiled perimeter. This can be done quite quickly with pneumatic hand-held hammers.
Other instruments that are worthwhile making if you are going to make more of the same panels is a buck. Made of timber, metal or fibreglass, a buck is a brilliant way to check the shape of the panel quickly and accurately, time and time again. Many bucks are built strong enough so that hammer forming around the buck is also possible and this adds great acceleration to the fabrication time.
Another very handy piece of equipment is a reciprocating hammer machine. Trumpf, Pullmax and Nibbler are all brands of machines that were around from the late 40s and are brilliant for shaping, swaging, folding, cutting, beading and adding louvers to panels. With clever tooling fabricated out of steel, aluminium or even Acetal plastic, just about any shape is possible. Even cutting out multiples blanks of the same panel including slots and internal cutouts is quite simple with these machines. The only problem is they are very hard to get a hold of, but don't worry, we have all of these tools and more with the age old skills and knowhow to use them.